As the weather gets warmer and we see more sunshine each day, we hope you get the chance to enjoy the season. From a baggage handling project at DEN to a new pipefitting fabrication shop in Pueblo and more, our teams have been busy lately. If you’d like to talk to us about your next project, please reach out.
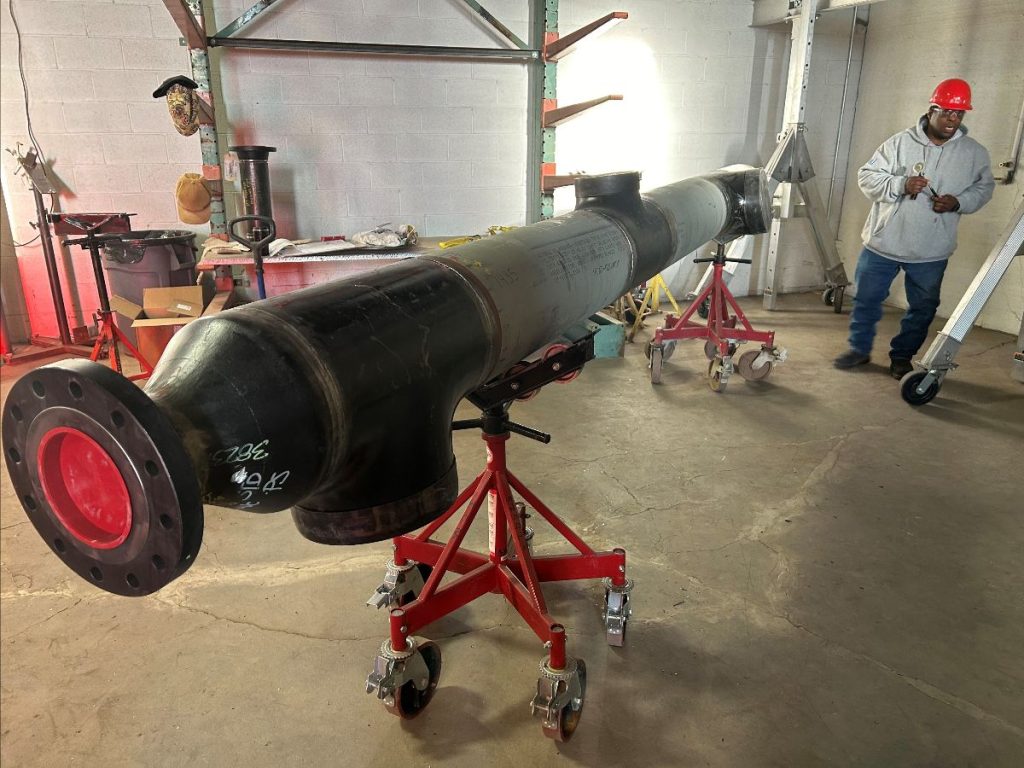
ICM Expands Pipefitting Capacity
We have acquired a new pipe fabrication shop in Pueblo to expand our pipefitting capacity. The new pipe fab shop employs 10 full-time pipefitters and can handle up to 48-inch diameter piping. ICM’s pipefitters are proficient at handling a wide variety of materials, including stainless steel, which is considered a more difficult material to fab and install.
Approximately 35% of ICM’s process piping jobs are now being prefabricated in the shop, which is the preferred way to build pipe given that it’s done in a controlled atmosphere that’s free of weather and eliminates other external factors that can otherwise delay a project. Read the full release here.
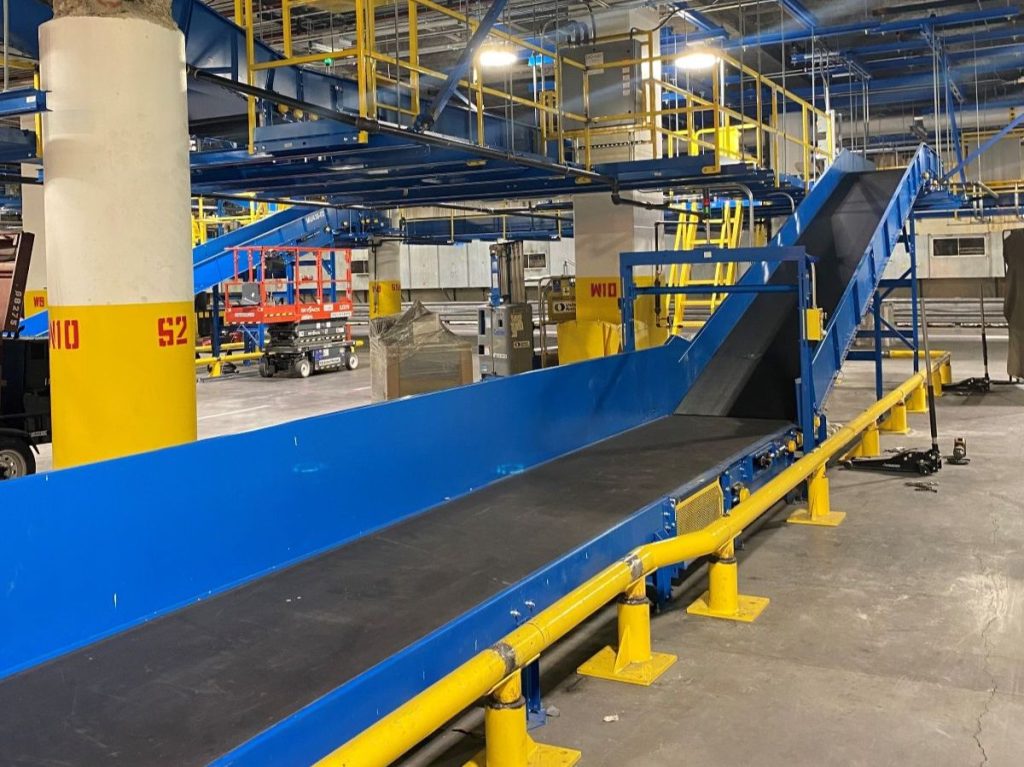

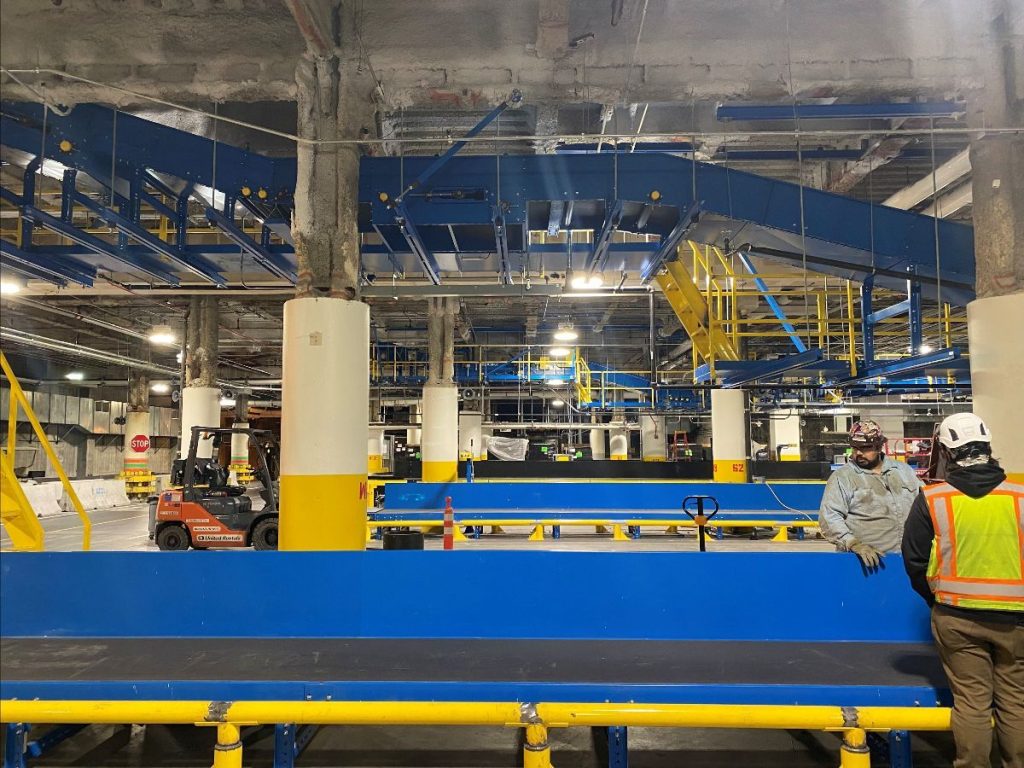
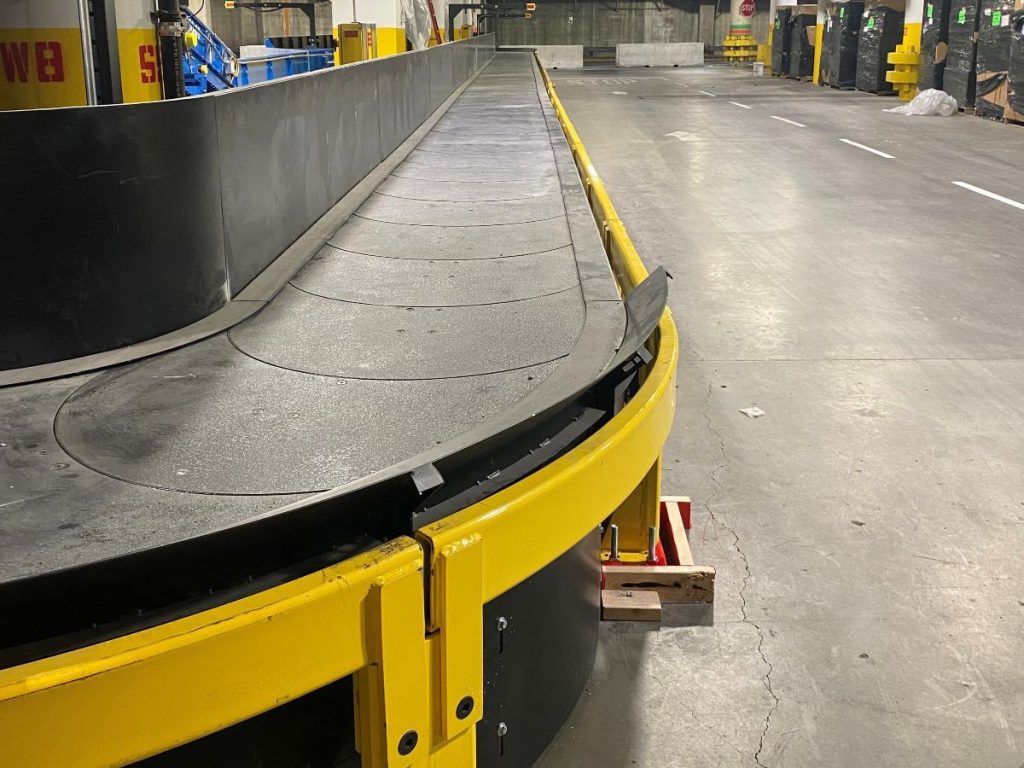
Updating DEN’s Concourse A Baggage Sortation
Denver International Airport (DEN) has begun using a new baggage sortation system in Concourse A and Concourse B, allowing bags to be transferred and sorted more easily and efficiently between the tarmac level and the basement. ICM was responsible for mechanically installing the new conveyor system, flat plate makeup carousels and associated catwalks, which will be used by United Airlines. Gilmore Construction was the project’s general contractor and Daifuku Airport America Corporation was the equipment manufacturer.
This project is a precursor to a much larger baggage sortation installation in Concourse A, which is expected to start 1st quarter 2025 and will take roughly two years to complete. These upgrades are all part of DEN’s overarching goal of increasing passenger capacity to 100 million passengers by 2025.
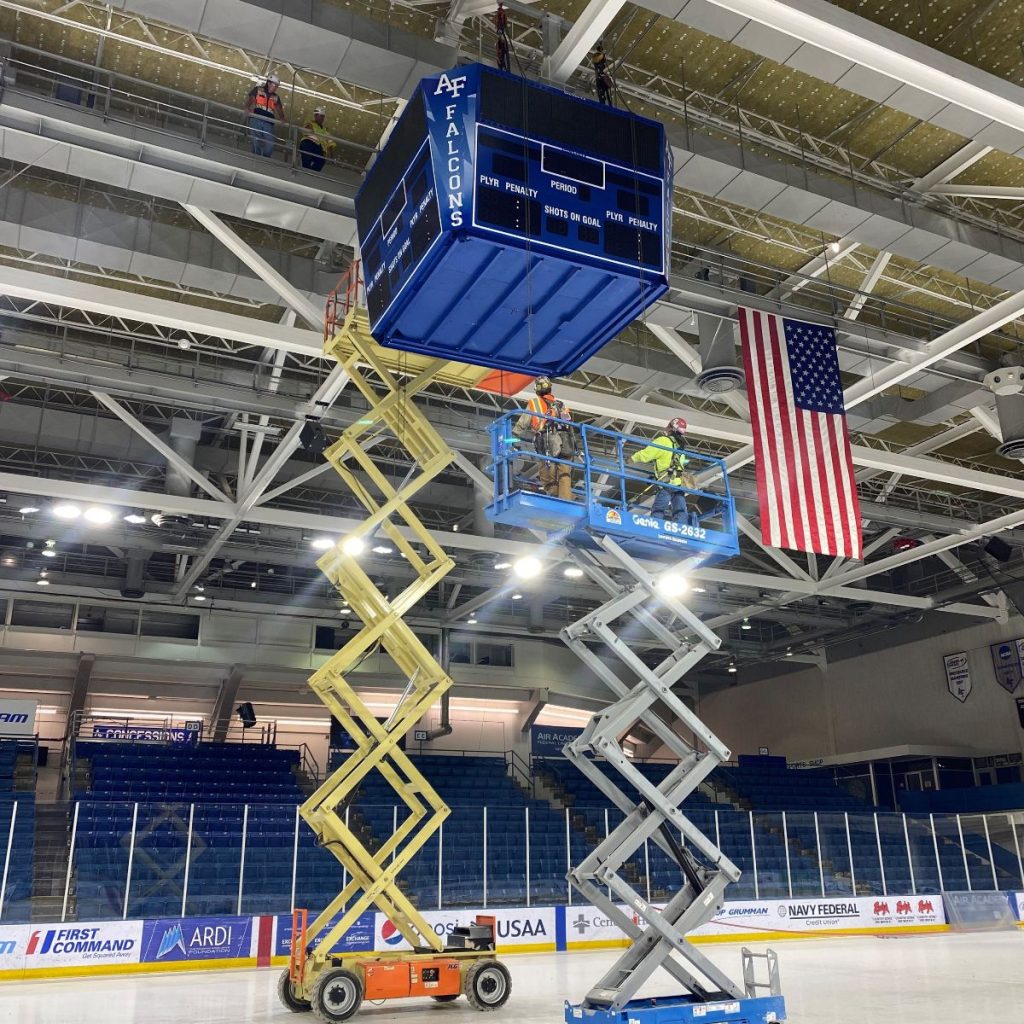
Renovating the Cadet Field House at the U.S. Air Force Academy
We recently helped complete phase two of the Cadet Field House athletic facility renovation at the U.S. Air Force Academy in Colorado Springs. The Field House was one of the academy’s original buildings built in the mid-1960s, and this was the first major renovation since its conception. The building houses the indoor track, basketball arena and ice hockey rink.
Our work included installing new basketball court flooring and goals, updating the hockey arena dasher boards, renovating locker rooms and replacing the entire HVAC system. We also worked on the new elevator that services all three floors in the building, we fabricated and installed structural steel for the new press box and ticket vestibule in the hockey arena, and we helped update the bleachers and hockey rink for ADA accessibility.
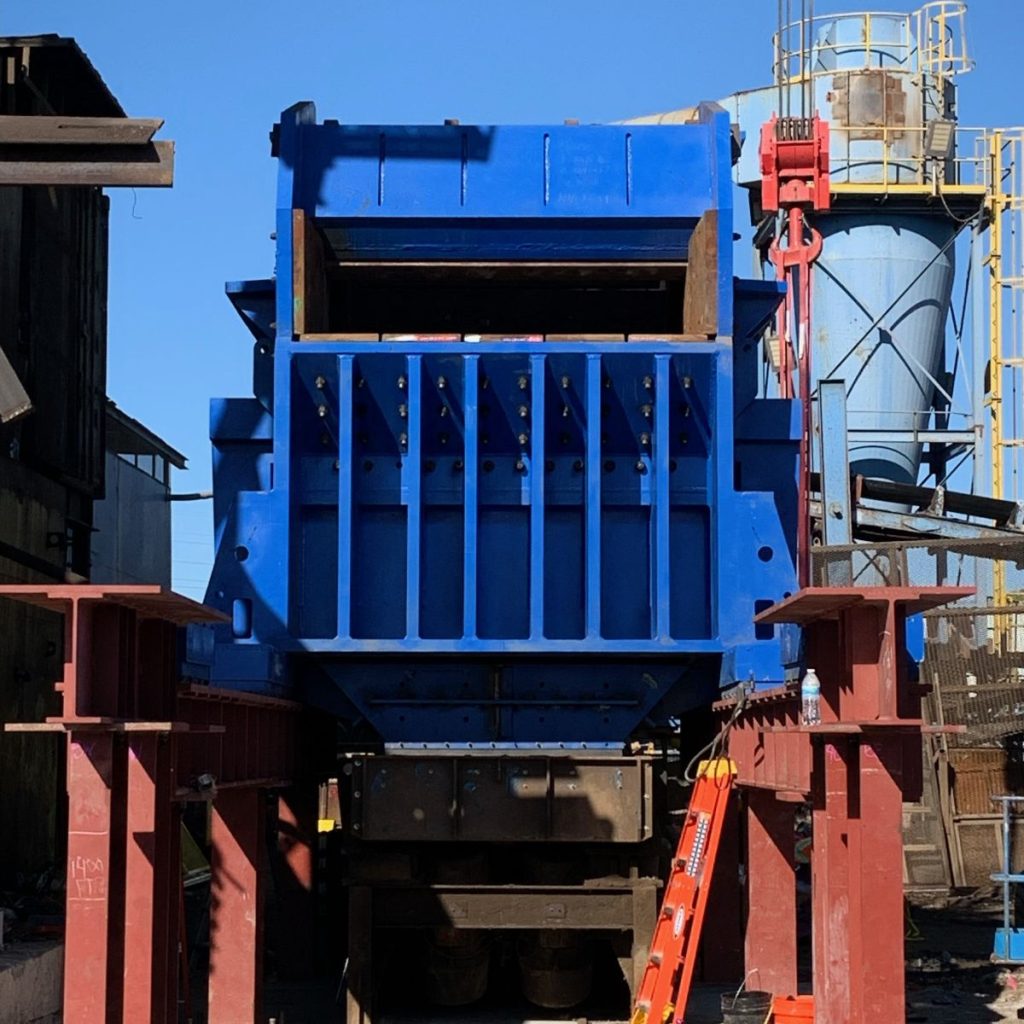
Overhauling the Car Shredder at Evraz
ICM recently overhauled the car shredder at the Evraz steel recycling plant, which is a combined weight of 600,000 pounds of equipment that can shred an entire car down into 1-2 inch diameter pieces.
ICM was hired as the general contractor for the project, responsible for the equipment removal for reuse, equipment demolition, foundation demolition, prep and compact subgrade, installation of helical piers, new concrete foundation, fabricating and erecting new structural superstructure, re-installing the equipment and new shredder, piping new hydraulic lines and installing new electrical, all back in its original position.
Demoing the equipment was challenging because it had to be disassembled in various parts and pieces, which weighed anywhere from 50,000 to 175,000 pounds. Following the demo, we installed the new concrete foundation and structural steel to support the equipment, then we put the new equipment back in the exact order it needed to be in. We were able to minimize the plant’s downtime to just 29 days. To achieve this, we phased the project so that various trades overlapped, work swing shifts were implemented and “rocket mix concrete” was utilized.
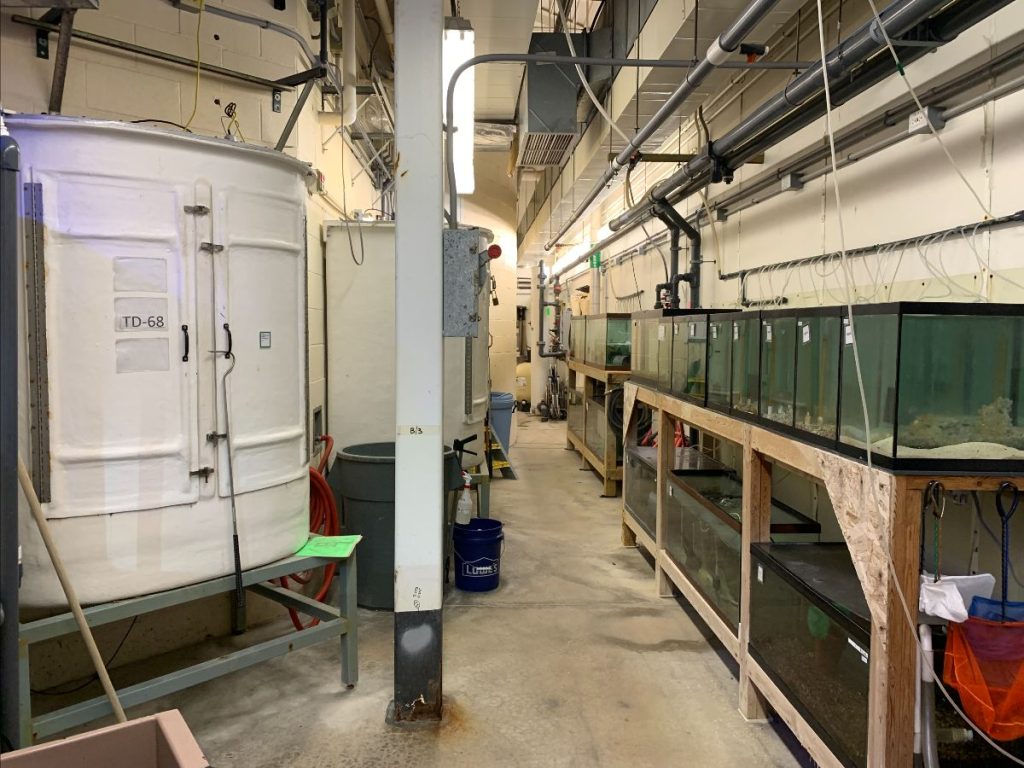
Reinforcing an Exhibit at the Denver Zoo
We recently finished up a project at the Tropical Discovery area at The Denver Zoo. We reinforced six columns in the back area of the exhibit. One column had a full base replacement in which we temp shored the existing column, cut out the base, replaced and reinforced.